Evergreens Insights : Les observations de Michel Wursteisen sur les défis de la durabilité
Dans cet extrait du podcast « Evergreens by Spuerkeess », nous partageons le point de vue de Michel Wursteisen, Responsable QSHE, Security & Compliance chez Wallenborn Transports S.A. sur l’importance de la durabilité et l’accompagnement des entreprises vers une transition énergétique réussie. Découvrez ses conseils pour une mise en application efficace et les stratégies qui permettent de construire une entreprise durable et résiliente.
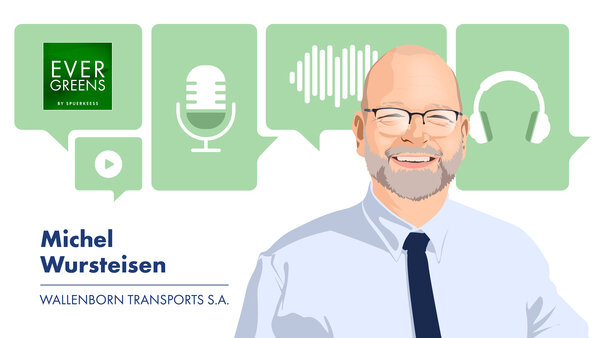